5S Method - A Clean Path to a Better Success!
“If you always do what you always did, you’ll always get what you’ve always got.” – Henry Ford
It should go without saying that people generally like to work in a well-organized and clean environment. A well-organized workspace can help workers to be more productive while reducing work-related stress and saving time (especially because employees spend significantly less time looking for tools and materials.) The “5S” methodology is a building block of a lean organization that was first proposed in Japan as a series of activities intended to foster an organized workplace. Implementing 5S is inexpensive, doesn’t require any technical analysis, and can be easily deployed in all types of companies, ranging from manufacturing plants to offices, small businesses, and large multinational organizations.
What Is 5S?
5S is a workplace organization method that was first popularized by Taiichi Ohno, who also designed the Toyota Production System. This simple yet effective organizational method is intended to eliminate Muda (waste) and can be summed up as a list of five Japanese words: Seiri (Sort), Seiton (Set In Order), Seisō (Shine), Seiketsu (Standardize), and Shitsuke (Sustain). The list of actions defines a simple process to organize a workspace for efficiency and effectiveness. Each of these five terms is expanded upon below:
Sorting – Sorting refers to the identification and removal of unnecessary items from the workplace. Cluttered workspaces often lead to unnecessary work, waste, and workplace injuries. The steps to sorting are:
- Establish criteria for what is not needed. For example, if something hasn't been used for 6 months, it may be a candidate for “disposal”
- Identify unneeded items and move them to a clearly-defined holding area
- Dispose of unnecessary items, either by transferring to a department that needs them, selling them, or discarding them
- Conduct an initial cleaning of necessary items
Set in Order Once the initial sorting is completed, the natural sequence is to get the work area organized. Set in Order is often described as ‘a home for everything and everything in its home.’ Items should be stored where the item can be most efficiently accessed when needed. Frequently-used items should be as close to where they are used as possible. The steps of simplifying are:
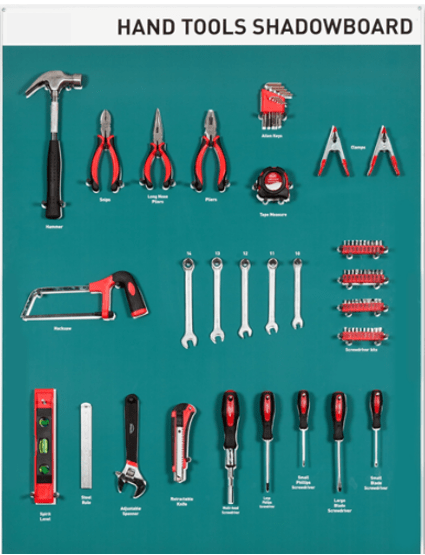
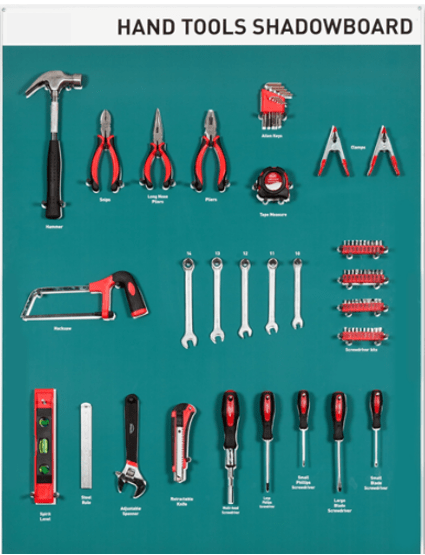
- Determine a location for each item based on the frequency of use and proper safety measures
- Develop “shadow boards” and label items to speed storage and rapidly identify missing items
- Determine how to most efficiently replenish supplies
- Document and train staff on workplace layout, equipment, supplies, and agreements for returning items to their designated homes
Shine – Shining refers to a systematic inspection and cleaning of a workspace to keep the area free of clutter, dirt, and debris. Dirty workspaces are proven to negatively impact employee perception/morale and lead to worsening conditions and safety hazards. A regular cleaning regimen makes the job of doing daily cleaning and inspections easier. The steps of systematic cleaning are:
- Identify inspection criteria and set a schedule
- Conduct daily cleaning and visual checks
Standardizing – Standardizing involves the establishment of a system for how the workplace and / or workstations should be maintained, inspected, and cleaned, in addition to assuring that everyone knows what is expected. It’s ideal to involve all affected employees when establishing the standards and everyone should have had some involvement in establishing the 5S practices in their work area. It is important to make 5S standards very clear and accessible to all employees. The steps of standardizing are:
- Document new methods/standards for maintaining work areas and for doing the work
- When possible standardize methods across similar work areas
- Establish a routine check sheet for each work area. The check sheet is like a pilot's pre- flight checklist. It shows what the team should check during self-audits
- Establish a multi-level audit system where each level in the organization has a role to play in ensuring that 5S is sustained
Sustaining – Sustaining is commonly thought of as “holding the gains” and is usually thought of as the toughest "S." Sustaining involves a regular evaluation of how 5S is being utilized in the workplace and the effectiveness of activities to ensure progress is not lost through progressive complacency. The steps of sustaining are:
- Document policies and train employees
- Perform routine 5S checks to ensure implemented policies are being observed
- Proactively address backsliding and identify new opportunities for improvement found during routine checks
Benefits of 5S.
While the rudimentary nature of 5S is often to blame for overlooking its undeniable benefits, this methodology is in place at a growing number of Fortune 100 companies around the globe. In addition to generating a positive ROI, ancillary benefits include Improved safety, higher equipment availability, lower defect rates, increased production, better agility and flexibility, improved employee morale, and better asset utilization, among others.
About MBC.
Midwest Business Consulting is a veteran-owned business specializing in helping clients achieve exceptional results through optimized operations and continuous improvement initiatives. To learn more about improving your organization’s operations and profitability call MBC at 708-571-3401 or visit us at www.getMBC.com.
Back to top
Download this article in PDF format
Back to Blog